高邮刀具涂层加工厂家
发布时间:2023-12-22 02:03:53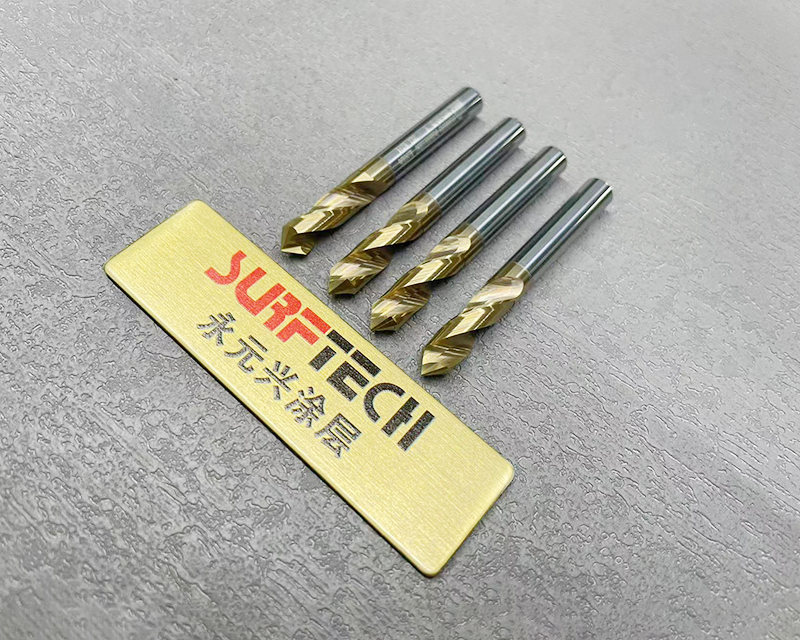
高邮刀具涂层加工厂家
PVD涂层对工件表面要求的工件或工具表面条件对涂层的性能有决定性的影响。优异的涂层质量如下。优质涂层工件需要研磨或抛光,并对运输进行防腐处理。一、磨削表面不能出现浅裂纹、氧化皮或再硬化烧伤。二、研磨过程中使用的冷却液不能含有磺酸钙、硼或碘化合物,或含硅的消泡剂。3、磨削表面、磨石磨削表面、抛光表面或磨盘磨削表面必须无磨料和残留物。首次使用时,刀刃必须无毛刺,以免断裂。五、在EDM电火花加工过程中,推荐多种表面处理方法,以减少白层的形成。6、表面必须是明亮的金属。腐蚀表面、棕色光制表面、蒸汽烧蓝表面或类似处理表面不能涂层。七、盲孔及内螺纹必须无硬化盐等污染物。八、碎屑、蜡、胶带、油漆等非金属杂质研磨粉清洗剂残留物,必须从工件上去除指纹和类似物。九、焊接接头和铜焊接头必须无气孔、焊剂和镉化物。十、工件要去磁。

高邮刀具涂层加工厂家
三,前处理,这个过程的使命是处理不同的基体。一般有玻璃珠喷砂和金刚砂喷砂。不同粒度的基体处理程度不同,选用的喷砂工艺取决于不同的基体原料。同时,关键的质量控制点是两人承认程序质量管理体系。基础数据的质量和清洁度在很大程度上决定了涂层的质量。确定涂层质量的规范有其外观粗糙度,其外观粗糙度在很大程度上取决于处理基础数据的外观粗糙度,因为薄膜数据的布置结构是模仿布置结构。涂层的目标是获得润滑的外观,以生产好的界面。四,清洗,本工序的主要使命是清洁涂层前的工件外观,去除外观上的异物,包括油污、重颗粒等。关键的质量控制点是清洁质量的控制,包括清洁剂的比例监控、清洁喷嘴的角度监控等。如果清洁后的目视检查仍然缺乏检查外观的清洁质量,可以添加外观能量检测,现在限于研发人员使用这种检测方法。

高邮刀具涂层加工厂家
为什么模具需要PVD涂层?1.模具涂层的高温性能。当模具进入较高的工作温度时,硬度和强度就会下降,导致模具早期磨损或塑性变形失效。因此,模具材料应具有较高的耐火性,以保证模具在操作温度下具有较高的硬度和强度。2.耐冷热疲劳性能。一些模具在加热和冷却过程中反复出现,导致模腔表面张力和压力变应力,导致表面开裂和剥落,增加摩擦,阻碍塑性变形,降低尺寸精度,导致模具故障。热疲劳是热作模具失效的主要形式,以帮助该模具具有高热疲劳性能。3.耐腐蚀性。一些模具,如塑料,在工作中,由于氯、氟、HCL、HF等强腐蚀性气体沉淀分解加热,模腔表面侵蚀,提高表面粗糙度,增加磨损故障。满足模具的技术性能要求。模具制造一般要经过锻造、加工、热处理、多道工序。为保证模具制造质量,降低生产成本,材料应具有良好的延展性、加工性、硬化性、淬火性和磨削性;氧化小、脱碳敏感性和淬火变形开裂倾向。
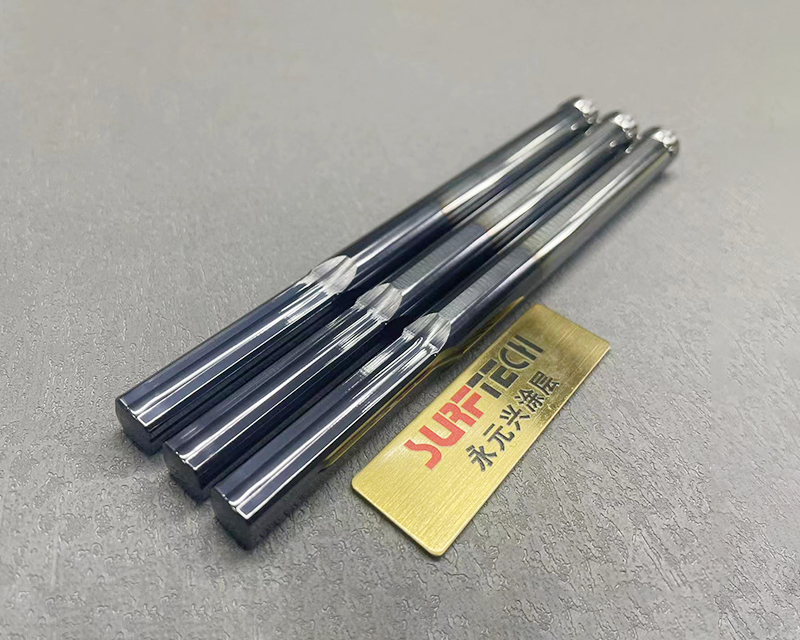
高邮刀具涂层加工厂家
压铸涂层加工中如何选择压铸设备?压铸是一种金属铸造工艺,主要特征是利用模腔对熔化的金属施加高压。模子一般是由较高强度的合金加工而成,这一工艺与注塑成型相似。多数压铸铸件是无铁的,那么压铸涂层厂家加工中如何选择压铸设备?1.根据产品特性选用适当的压铸机。““马拉小车”式的压铸加工常常意味着大量的能源浪费。2.选择压铸设备,要比较能源效率参数,选择节能的压铸设备,可以节约能源20-80%。3.利用电磁感应加热、红外线加热等新型加热技术,可达到20-70%加热节能。4.对于加热,冷却系统有有效的隔热保温措施,以减少热,冷损失。5.保持设备传动部件良好的润滑,减少因摩擦增大或设备运转不稳定而增加能源消耗。6.液压油要与压铸机选配,减少液压系统作业能耗。7.使用先进的压铸加工技术,可以大大提高节能能力。8.对现有传统铸造机械进行多种节能改造,降低能耗。9.定期保养设备和加热冷却管道,确保管道内没有杂质,水垢堵塞等,达到设计的加热效果,冷却效率。10.确保压铸机在正常工作状态。加工过程不稳定,会造成二次产品的产生,能量消耗增加。

高邮刀具涂层加工厂家
压铸涂层有什么优势?纳米涂层在压铸模具中的作用:增寿、增硬、增值,并以其硬高度、高耐磨、强抗腐蚀性、抗高温、抗黏着性等优越的使用性能广泛应用于模具工业中。在压铸行业,因为在每个压铸循环初期,模具型腔要承受炽热熔融合金的急热作用,工作表面会产生压缩热应力;压铸结束后要在模具内喷润滑剂,进行急冷,因而又在其表面产生拉应力。在这样的交变热应力作用下,模具表面会产生热疲劳微裂纹,随着压铸循环次数的增加,微裂纹急剧扩展,有的向心部扩展,形成龟裂纹。如果在裂纹周围同时伴随有熔融合金对模具型腔的冲刷及腐蚀,模具表面还会进一步损坏,终造成模具的早期开裂甚至报废。压铸过程中的粘模、冲蚀、腐蚀而造成的产品废品率高,生产效率低下,甚至造成模具的损坏等问题一直是困扰各压铸企业的重大难问题。