温岭刀具涂层生产厂家
发布时间:2023-11-02 02:06:39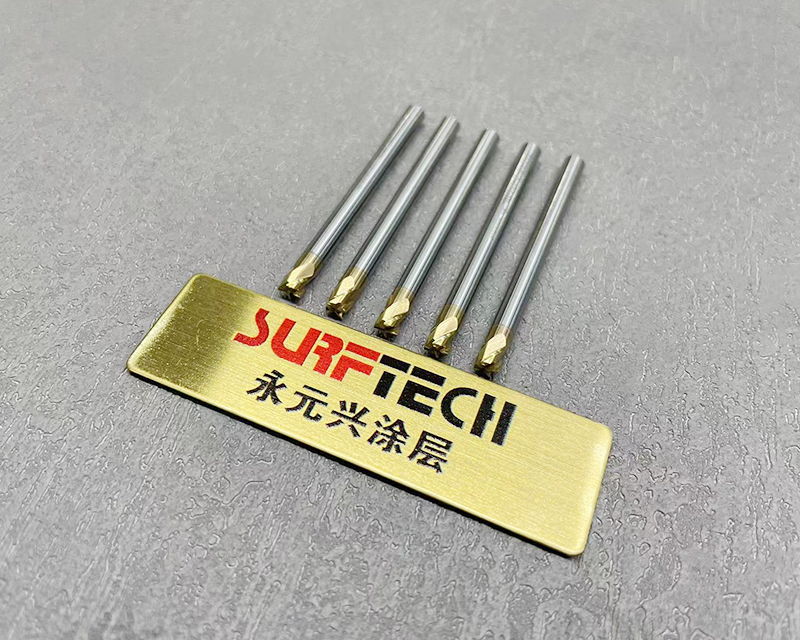
温岭刀具涂层生产厂家
PVD涂层使用喷砂工艺对质量的影响。根据工艺目的,喷砂可分为:(1)表面清洁(2)刃口细化(3)改善钴损失表面(4)涂层后的处理。根据喷砂工艺方法,可分为干喷砂和湿喷砂。根据操作方法,可分为自动喷砂机和手动喷砂机。大多数干式喷砂机配备自动喷砂功能和手动喷砂功能。自动喷砂用于处理滚刀、钻头、插刀等数量大、形状规则的标准工件;手动喷砂用于处理模具等特殊工件。干式喷砂机使用的砂有B4C、SiC、Al2O3(金刚砂)、Si02(玻璃珠)、钢珠、塑料颗粒等。B4C和SiC颗粒太硬,切削力强,喷砂时间稍长,工件尺寸可能超差。此外,工件表面可能会产生额外的冷压,增强应力,涂层更容易剥落;玻璃珠虽硬但脆,易碎,磨损快,使用寿命低;钢珠容易生锈污染工件,塑料颗粒容易粘在工件表面。这两种情况都不容易清洗,增加了涂层质量下降和程序中断的风险。此外,塑料颗粒的切削力太小。对硬质合金几乎没有影响。因此,最适合选择A1203(金刚砂)作为喷砂介质。当然,对于特定的工件,可以选择更合适的喷砂材料。
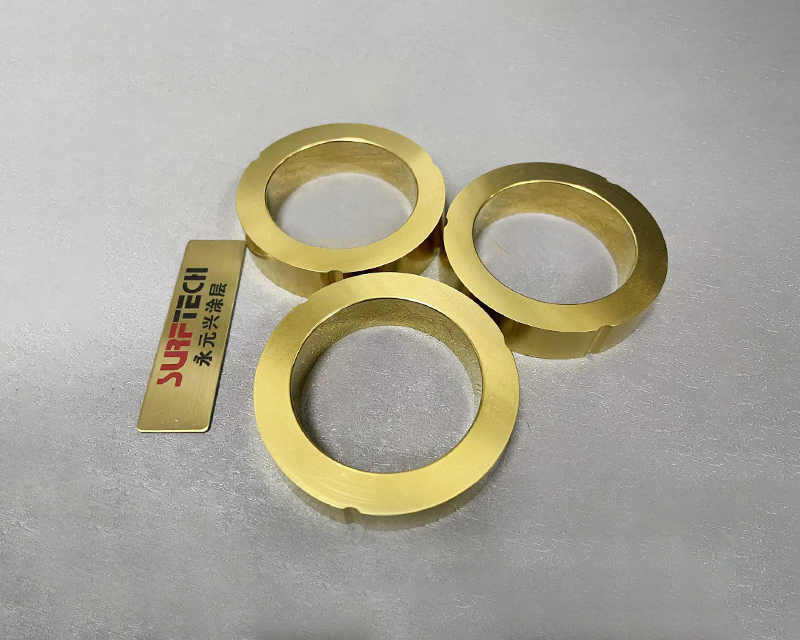
温岭刀具涂层生产厂家
真空涂层机PVD涂层技术适用于各种加工要求和工件材料的高速钢和硬质合金工具。它的优点和特点是什么?以下是小编的详细介绍:1.技术特点。(1)PVD膜层可直接镀在不锈钢和硬质合金上。对于相对较软的锌合金、铜、铁等压铸件,应在适合PVD之前进行化学镀铬,但水镀后容易起泡,不良率高;(2)PVD涂D涂层加工温度在250℃~450℃之间;(3)工艺时间由涂层类型和厚度决定,一般工艺时间为3~6小时;(4)PVD涂层层厚度为微米,厚度较薄,一般为0.3μm~5μm,其中装饰涂层层厚度一般为0.3μm~1μm。因此,在几乎不影响工件原有尺寸的情况下,可以提高工件表面的各种物理化学性能,保持工件尺寸基本不变,镀后无需再加工;(5)PVD技术不仅提高了涂层与基材的结合强度,而且从第.一代Tin发展为TiC.TiCN.Zrn.Mos2.TialN.TialCN.Tin-AlN.CNX.DLC和Ta-C等多种复合涂层,形成不同颜色的表面效果。(6)目前的颜色为深金黄色、浅金黄色、咖啡色、铜色、灰色、黑色、灰黑色、彩色等。通过控制涂层过程中的相关参数,可以控制涂层颜色;涂层后,可以用相关仪器测量颜色值,以确定涂层颜色是否符合要求。
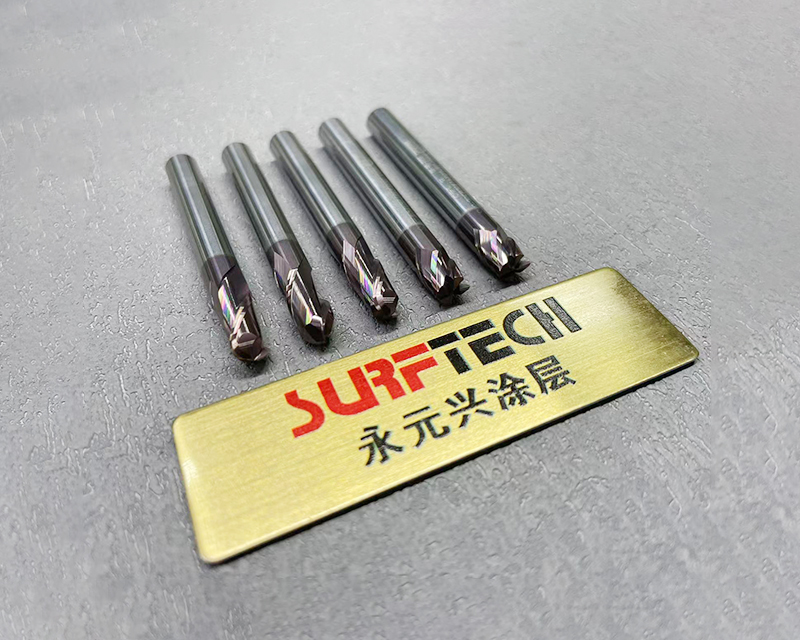
温岭刀具涂层生产厂家
五、操作涂层工艺,PVD涂层过程包括抽真空-加热-蚀刻-涂层-冷却。同时,使用程序软件进行自动控制,要求程序软件自动记录基础数据的温度、阴阳极电压参数和真空度的变化,以便于后续的可追溯性。PVD从基体温度、气压、沉积率等参数的变化可以看出涂层的质量。真空设备在很大程度上影响涂层质量,需要确保涂层环境稳定、清洁,如果涂层环境混合污垢或过多飞溅颗粒,将严重影响涂层结构和质量,所以清洗作业前非常重要,夹具定期维护需要更加注意,炉腔电气元件检查尤为重要,最后一批残留气体检查也非常关键。六,后处理,根据涂层产品的应用环境,可以选择后处理,提高外观的光洁度,也可以对产品进行退磁处理,避免加工铁屑的粘附倾向。
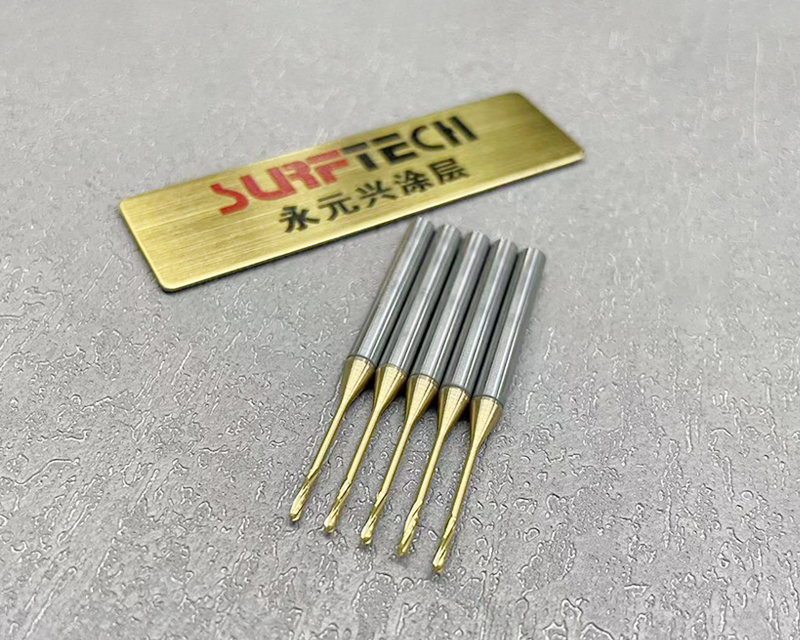
温岭刀具涂层生产厂家
PVD涂层外表常见的缺点处理:1、真空抛光处,真空腔体以及内部部件的气体放出量,和材料的外表积直接相关。固体外表的原子密度大约为2×1019 m-2,考虑到外表的高低不平,实践的固体外表会吸附大量的气体分子。通过抛光使外表更加平坦,能够大大减小外表积,从而削减外表吸附的气体分子。抛光主要有玻璃丸喷砂和电解抛光两种手法。2、超声波清洗,超声波清洗是使用超声波在液体中的空化效果、加速度效果及直进流效果对液体和污物直接、直接的效果,使污物层被涣散、乳化、剥离而到达清洗意图。向液体导入超声波后,液体的激烈运动使局部发生压强差。压强低的部分会发生大量的气泡,当压强从头升高时,这些气泡会在瞬间决裂,从而在液体中发生冲击波。冲击波会将固体外表的油污剥离。超声波清洗用的液体一般采用酒精或丙酮。通过超声波清洗的部件放到大气中后,酒精或丙酮会马上蒸腾,不会在部件外表留下水垢。

温岭刀具涂层生产厂家
增加聚氯乙烯涂层的基础温度可以去除挥发性残留物,增强表面扩散和再结晶能力。界面反应加速,底部杂质扩散。基质融化。增加晶体颗粒的大小。根据工件的金相结构、热处理和几何形状,促进再结晶界面的延伸和生长,降低内应力,提高阶梯覆盖率,提高与衬底相互作用所需的涂层温度,如锐边、薄板等。电弧电流、底部偏压和反应压力也会影响温度。涂层可以从180℃开始。工件应在不引起材料物理变化的温度下涂层。PVD涂层工艺对环境无不利影响,符合现代绿色制造的发展方向。目前,PVD涂层技术已广泛应用于硬合金立铣刀、钻头、台阶钻、油孔钻、铰刀、丝锥、可转位铣刀、异形刀、焊刀等涂层处理。PVD技术不仅提高了薄膜与工具基材的结合强度,而且将第.一代氮化钛的涂层成分发展成碳化钛、TiCN、氮化锆、氮化铬、二硫化钼、氮化钛、氮化钛铝、氮化锡、氮化碳、金刚石碳、钽碳等多组分复合涂层。